rohan wanchoo
product manager
my role
I work as a Technical Product Manager for Siemens' flagship software for Simulation Process and Data Management (SPDM), Teamcenter Simulation (TcSim). My team and I are responsible for its development, marketing, outbound/inbound support and strategic planning.
To understand SPDM, we need to take a step back and first understand Computer Aided Engineering (CAE). Simply put, its the use of computers to perform engineering analysis and predict how a given product will behave in real time conditions. For example, automotive customers such as Daimler, or Ford use CAE tools to design the shape of their cars. Aerospace companies use it to predict the loads and stresses on aircraft wings. Turbine manufacturers such as Siemens or G.E use CAE tools to design turbine blades. Biomedical companies use them in the development of devices such as stents and heart pumps. These are just a few examples. CAE simulation is a relatively new field (~70 years) but its usage has been steadily growing and has become an important part of the product development process for many companies.
Before CAE simulation became the preferred choice, companies relied on on-premise physical testing. In fact some companies still do. Although these techniques are more accurate, they are time consuming and expensive. Now, with a deeper understanding of physics, development of superior mathematical models and increased computational power, companies can use CAE tools to accurately predict the specifications of their product design that would reduce cost and provide most value to customers. Performing CAE simulation is faster and cheaper which in turn allows companies to validate or test thousands of designs in a short period of time.
Due to these and many more benefits, we have been seeing a steady rise of CAE simulation market. It is one of the rapidly growing segments of PLM and is expected to reach $11 billion in 2023. Siemens Digital Industries boasts a wide range of simulation and modeling tools such as NX, STAR-CCM+, Simcenter 3D,etc. Here is a list of simulation tools developed and sold by Siemens DI.
Now, let's come back to SPDM. With this increased usage of CAE simulation, companies face several business challenges such as inefficiencies in product development, lack of data traceability and poor collaboration to name a few. This is where SPDM comes in. To overcome these challenges, companies employ an SPDM tool such as TcSim. As described by NAFEMS, an SPDM tool is “a technology which uses database solutions to enable users to manage structures of simulation and process data across the complete product lifecycle. SDM artifacts can be data, models, processes, documents, and metadata relevant to modeling, simulation, and analysis.”
teamcenter simulation (tcsim)
As indicated earlier, TcSim is a popular SPDM software used by companies around the world. It is a module of the Siemens' flagship product lifecycle management (PLM) software Teamcenter. Teamcenter is available to customers through its traditional desktop version and a web browser version called Active Workspace. Active Workspace, with its simplified UI, makes it easier and less cumbersome for technical and non-technical users to navigate through the PLM system. It does not require any additional installation and is easily accessible to its users.
TcSim has been specifically designed to allow companies overcome challenges described above and gain complete control of their CAE simulation process and data. TcSim offers several benefits, some of which include:
-
Support of increasing volume and complexity of simulation work through data and processes management
-
Increased confidence in simulations due to complete traceability from requirement gathering to design and validation.
-
Speed up of simulations through better collaboration, improved time to find data and greater re-use of existing work.
-
Fast delivery of results due to standardization and automation of simulation processes.
-
Greater visibility into the simulation process and results for program management and downstream operations.
-
Improved flexibility through managed and standardized access to third party simulation tools.
-
Lower implementation costs and risk by leveraging the proven Teamcenter platform as the common infrastructure solution.
projects recently worked on
Here are some cool features I had a chance to work on recently.
automatic extraction of key performance indicators (KPIs)
goal: Provide users the ability to quickly and automatically extract KPIs from their simulation result files.
about the idea: Build an out of the box tool within TcSim that will allow users to extract KPIs from simulation result files stored inside TcSim. The extracted KPIs will be populated and visible to users in the KPI table. This feature is available on desktop (RAC) version 12.3 and web browser (Active Workspace) version 4.3.
why are we doing this: Users often need to obtain key result quantities (KPIs) from different simulation results to (1) understand if a specific design meets performance requirements (2) do a quick and easy comparison of different designs (3) search for simulation results based on KPIs, (4) leverage them in simulation reports etc. Previously, users had to manually download the result, extract KPIs and document them. This new feature, embedded inside TcSim, will perform the KPI extraction automatically saving engineers lot of time thus helping them make informed decisions faster. This will in turn reduce the product development time and help them get to their optimum design faster.
feature: Developing this feature required inputs from other product managers, providing detailed specifications and close collaboration with the services and development teams. We were able to successfully roll out this feature in 1 dev cycle i.e. 3 months. We plan to present this feature and overall KPI management solution at CAASE 2020 in Indianapolis
analyst workspace
goal: Provide CAE analyst users with a simplified user experience inside Active Workspace (AW)
about the idea: Design an out of the box workspace inside AW primarily targeted towards CAE analysts. This new workspace will only include commands and options that are relevant to the CAE analysts.
why are we doing this: Customers have increased adoption of Active Workspace (AW) primarily due to its ease of use and availability. However, CAE users have complained that several commands and options inside AW, albeit required, are used infrequently in mainstream CAE workflows. Moreover, the number of commands exposed can be overwhelming and make the whole experience difficult. Hence, we decided to come up with a specialized "Analyst Workspace" inside AW that will have limited but relevant set of options and commands relevant for CAE analyst users.
feature: As an example, below are snapshots comparing the home page and object page between Default and Analyst workspaces.



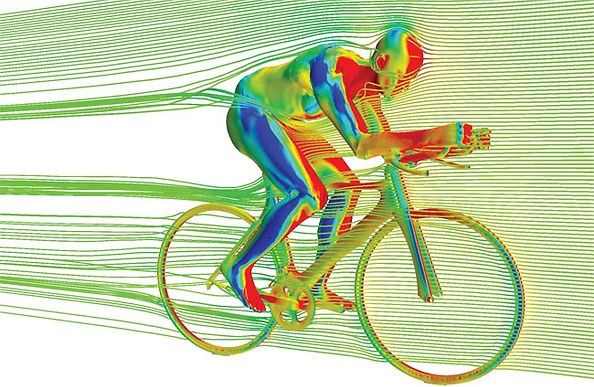
top: simulation of dust particles coming from wheels of a car traveling down the road in star-ccm+ (link).
bottom left: structural performance analysis of wing design (link)
bottom right: pressure fringe plots and streamlines simulating a racing bicycle in a wind tunnel. (image courtesy of felt bicycles)
simulation process and data management

KPI table in Desktop version (RAC)
KPI table in web browser version (Active Workspace)



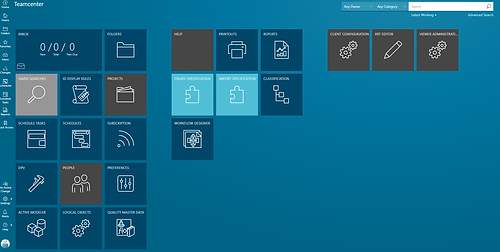
desktop
web browser - active workspace

home page (default)
home page (analyst)

business object page (default)
